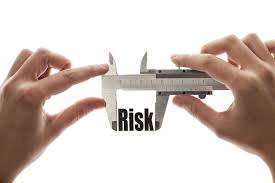
Based on the identified parts and processes from the prediction TopX those parts and processes must be mitigated until the agrees Manufacturing part quality is achieved. There are only two failure sources. The first one is the design where component choices leads to failures or design documentation which is not complete or even incorrect. The second source is the manufacturing process which is mediocre or even poorly executed .
Design caused manufacturing risks
By selecting a part there are two contributions to the product quality.
- Part Quality
- Associated processes coupled to the part
Part Quality
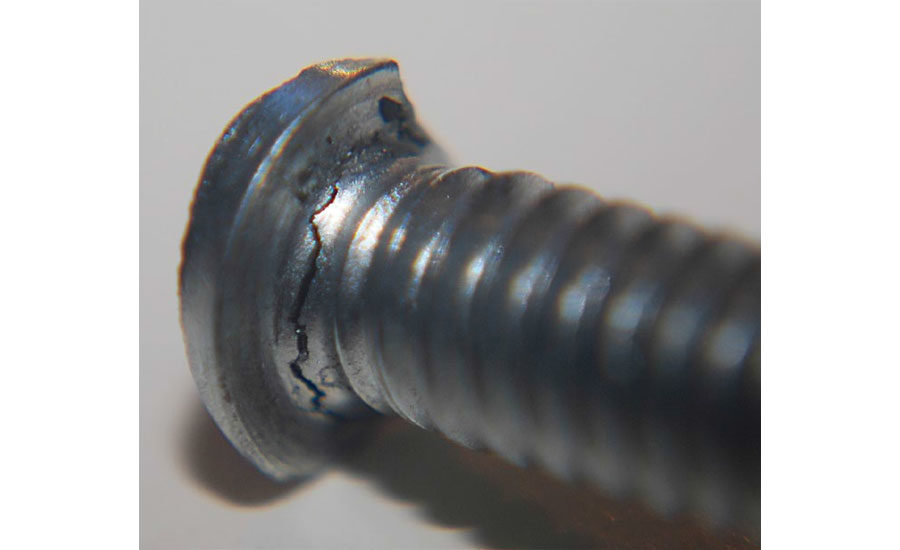
Part quality is determined by de part manufacturer. The part manufacturing processes used will result in the final part and every manufacturing step which is not executed perfectly contributes to the final part quality. Part quality is mostly specified in DPMO.
Associated processes coupled to the part
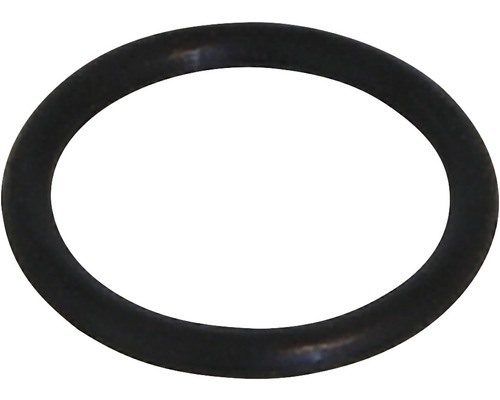
By selecting the part also the associated processes are contributing to the manufacturing risks. Associated processes are always placement of the part and for some also the connection they will make. Better to know upfront during the design phase what the contribution of those processes are. Knowing those risk can help to design differently.
Design incorrectness or incompleteness causing manufacturing risks
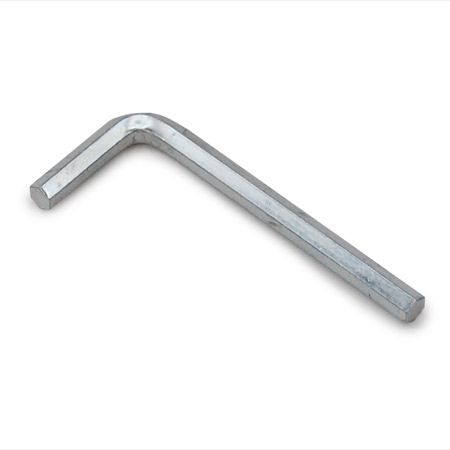
By not complete design documentation the manufacturing process can be implemented in a wrong way. Examples of this are not specifying the torques of bolts, nuts and screws. mostly the fasteners are based on best effort of the operator. This result in variations in the tightening process which results in a product failure in time. Other examples are the reflow process in electronics where combinations of parts leads to a faulty solder joint which also will come out during use of the product. The method applied here is that there is a database behind the mitigation model used which identifies those risk. This can already be done during te design phase.
Manufacturing risks
When the design is finished and all updates are secured the remaining risks are the be solved. There are three strategies which will lead to a reduction of the Infant Mortality defect rate (IMDR).
- Design change
- Process change/improvement
- Testing
Design Change
When changing the design by avoiding the associated process(es) which contribute to the risk this will lead to a new design with a new TopX.
Process change/improvement
When a process is the main contributor and a design change is not possible the process can be changed or improved. Changing can be going from manual to automated. Improvement of the process can be having the process better under control by redesigning the manufacturing process.
Testing
As last resort testing is the option. Be aware that testing produces a but also generates rework or even scrap.
Embedding the manufacturing process
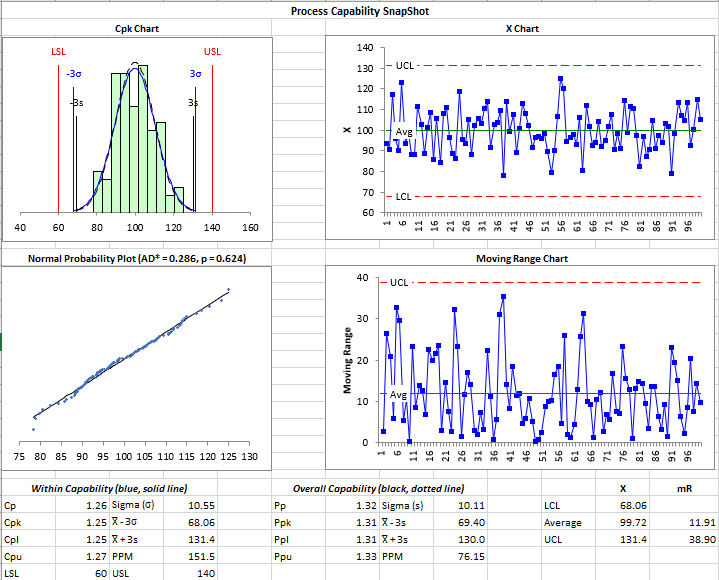
When having implemented those changes/improvements a method has to be developed to secure the product quality. A number of good methods are available. Static process Control (SPC) is one of the most used. Start measuring, define your acceptable process limits and monitor those.