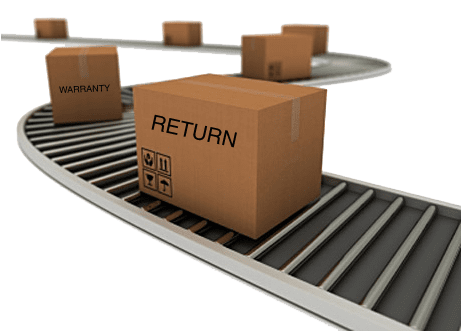
The Product Quality perceived by the user of your product is divided in three periods. Most important is the first impression of the product where when receiving and unpacking it the product should be according expectation. When this is not the case this can be that the product is damaged or doesn’t meet the requirements. For consumer products there is a warranty period which covers the first period where the product can be returned when something is wrong. For the not commercial products such as an EMS or Contract manufacturer the expectation is the same and the product should be according the agreed specifications. This first period is called the Infant Mortality phase and is mainly caused by the manufacturing processes used.
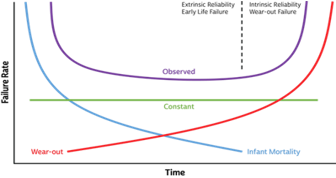
Constant Failure Defect Rate
The second period is when the customer is using the product. This period represent the time where the product is functioning according expectation. Nevertheless a failure can occur resulting in a defect product. This period stretches until the product is reaching the end of it’s commercial or designed life. This period is called the Constant failure rate.
Wear Out Defect Rate
The last period is when the commercial or designed life stops and more a more failure manifest itself. This period is called the wear out phase and the product will not functioning at all any more.
This means that there must be an agreement on life expectation, failure rate acceptance during normal life and most important the acceptable number of failures during the first year of use.
The life expectation could be define in a number of actions such as the number of washes a washing machine can perform during it’s designed life or a number of years a product must function.
Product Quality Design
The constant failure rate must be designed is such way the the warranty cost and customer expectation are met. The question is what is an acceptable constant failure rate or in other words how many returns you can accept. Is it 1 out of 100 products which can be returned or 1 out of 10000 during the warranty period. This is an financial trade of which must result in an healthy business discussion. This result in a designed constant failure rate in … hits/product/year.
Example: warranty period is 3 year and the number of return rate is 1:30000. This means a return rate per year of 1 out of 10000. This is 0.0001 hits/product/year.
Manufacturing Quality Design
The Infant mortality failure rate must be in line with the constant failure rate. This infant mortality rate will mostly occur in the first year of use and should be not larger than 10% of the Constant failure mode.
Example: Constant failure mode is 0.0001 hit/product/year. Infant mortality defect rate = 0.1 * 0.0001 = 0.00001 hit/product or 10 DPMO or 0.001%.
Based on your required part quality the design (Constant and wear out) and the manufacturing (Infant Mortality) should be result in a product which meet the customer expectation.
How to reach the required manufacturing Quality
The modern world is moving faster and faster and learning how your product behaves when it is out there takes too long. Your next product introduction will suffer from the part quality issue from your products introduced in the past. Another way to secure the required product quality is to predict the manufacturing quality based on the selected manufacturing processes and already mitigate the identified risks found during the prediction.