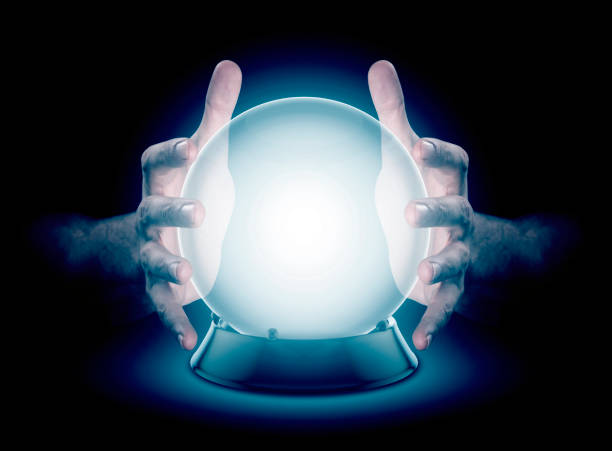
Prediction of the manufacturing risk is done with a method where all parts, processes and the associated failure frequency is being used. The principle behind this method is that if you have the Bill of Material (BoM) of a product you also can derive the Bill of Processes (BoP) very easly out of the product documentation. All processes used to manufacturer the product are coupled to a part in the BoM. If for every part in the BoM the process(es) are known a complete list of all processes used is created. Based on the quantity in the BoM the number of used parts are known automatically results in the number of processes. When also the frequency of the failure of the part or process is known the outcome is a to be expected manufacturing caused failure rate of the product.
Bill of Material (BoM)
A BoM consist out of 3 types of parts which have a different behavior in this method.
- Vendor Parts
- Manufactured Parts
- Assembled Parts
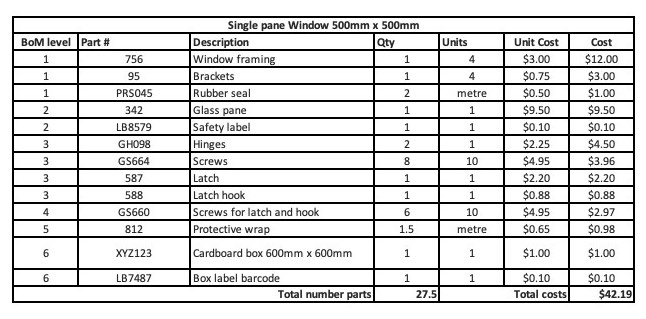
Vendor Parts
Vendor parts are parts which are bought and are not manufactured or assembled by the product manufacturer. As a result the part quality is what you buy. A method for determining the frequency of failures is using the performance of this product from the past or ask the manufacturer of this product for its failure frequency. The unit of measurement is either in % or ppm or DPMO. The processes coupled to a vendor part are assembly processes. The assembly process(es) consist always of a placement process and sometimes a connection process.
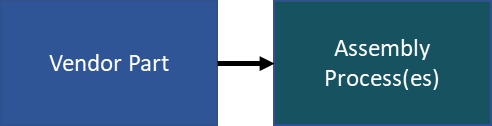
Examples:
Bolts, screws, nuts:
- Placement process and a tightening process.
- Failure frequency is based on the class bought.
Electronic parts (resistors, capacitors, inductors, active parts, …)
- Placement process and soldering process.
- Failure frequency based on manufacturer performance.
Manufactured parts
Manufactured parts are made out of one material and undergone a set of manufacturing processes followed by the assembly process(es). Manufacturer processes are milling, drilling, deburring, surface treatments, threading, … Assembly process(es) follow the same structure as for the vendor parts. Here the part quality is based on the capability of the manufacturing processes. This can be measured in Cpk, Ppk, ppm, …

Assembled parts
Assembled parts follow the same flow as the manufactured parts with as difference that the manufacturing processes are now testing, adjusting, cleaning, .. Part quality now is the contributions of all processes and parts which are used for the assembled part.
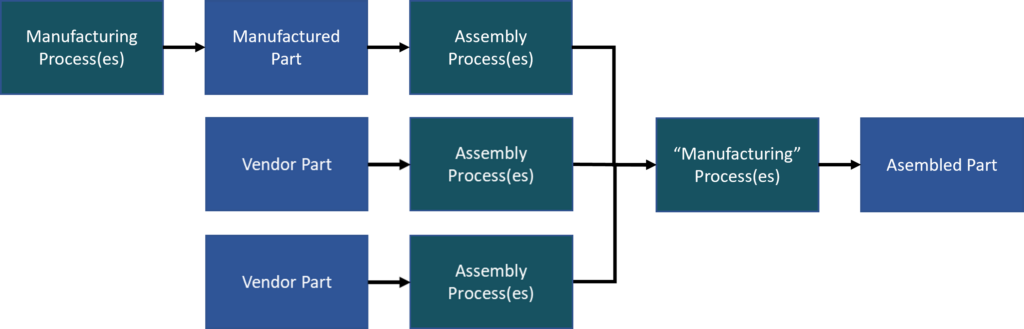
Predict manufacturing defect rate
Based on the parts and processes which are used to manufacturer and assemble the product a BoM/BoP can be created. When for each part and process the frequency of failure is used from the past a data based prediction is made. Crucial for the quality of the prediction is the failure frequency of the parts and processes.
The failure frequency is not always known by the product manufacturer. As a starting point industrial standards can be used and later replaced by the real manufacturer process capability. The calculation model used for the prediction is not adding all failures to an outcome but uses a statistical approach.
Severity
The failure frequency is also influenced by the product use or the effect the failure has on the product function.
Example:
The severity of the failure is influenced by the use. An example is that if the product is used in a static environment it will behave differently than in a dynamic environment. (temperature cycling, movement, ..). An other example are the decoupling capacitors on a Printed Circuit Assembly (PCA). If one or more a missing will this influence the functioning of the PCA. Both scenario’s can be adjusted with an severity.
Prediction outcome
Prediction outcome is a TopX list of all the to be mitigated risk either parts which are bought or processes used for manufacturing and assembly.
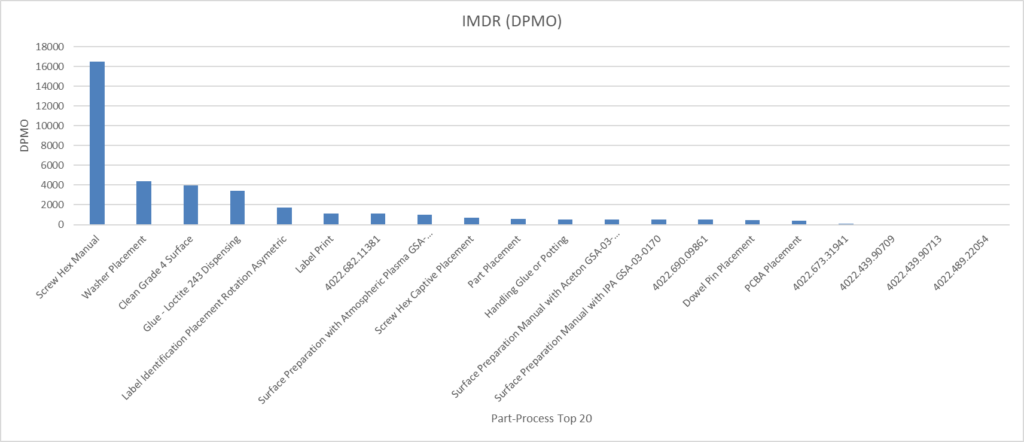
note: This behavior is also know as the Infant Mortality defect rate (IMDR) of a product. Even if the product is manufactured perfectly there is also the Constant failure rate. In the end the product will also reach its end of its commercial life. Constant failure mode is not influenced by the manufacturing but is a design risk. Wear our is influenced by the product usage and the design should be done in a way the product can reach its intended life span by the the expected usage.
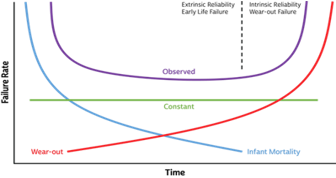